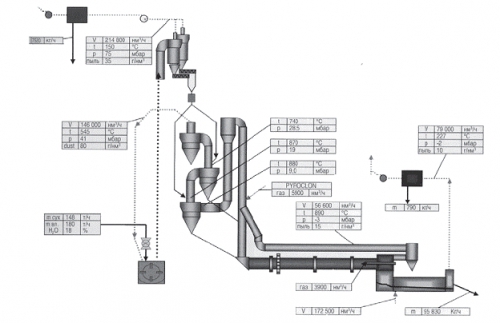
Рис. 4. Печной агрегат с дробилкой-сушилкой (KHD) Одной из самых эффективных схем комбинированного способа производства, получивших наибольшее распространение, является схема, при которой полученный в пресс-фильтрах кек подсушивается отходящими печными газами с одновременным помолом в молотковой дробилке-сушилке (рис. 5), работающей синхронно с вращающейся печью. В цементной промышленности такая компоновка оборудования работает уже более 25 лет. Печной агрегат с одной дробилкой-сушилкой может достигать производительности до 3500 т клинкера в сутки с расходом тепла на обжиг 950…1000 ккал/кг клинкера и расходе электроэнергии на весь печной агрегат 25…30 кВт•ч/т. При этом качество клинкера соответствует качеству клинкера, полученного при мокром способе производства. Одним из энергоемких процессов в технологии производства цемента является помол. Наиболее распространенной установкой доля помола является шаровая мельница. Однако данные мельницы ограничены производительностью по сырью, которая не превышает 300 т/час. Удельный расход электроэнергии составляет 15…25 кВт•ч/т на сухом сырье. Все большее распространение в мире для помола сырья находят вертикальные мельницы, производительность которых достигает 800…960 т/ч при удельном расходе электроэнергии 15…20 кВт•ч/т. Такие мельницы обеспечивают производительность печного агрегата до 12 000 т/час клинкера. Имеется информация о применении для помола сырья горизонтальных мельниц при удельном расходе электроэнергии до 15…20 кВт•ч/т. Основной технологической операцией, определяющей качество производимого цемента, является тонкий помол клинкера и добавок. В России основным помольным агрегатом является шаровая мельница. Производительность этих мельниц достигает 90…100 т/час при удельном расходе электроэнергии 38…45 кВт•ч/т при производстве цемента марки 500. Повышение эффективности помола клинкера возможно при переводе этих мельниц в замкнутый цикл с применением динамических сепараторов. При этом помимо повышения качества цемента возможно снижение удельного расхода электроэнергии до 32…34 кВт•ч/т. Установка пресс-валкового измельчителя позволяет на 30…40% повысить производительность шаровой мельницы и снизить удельный расход электроэнергии до 28…29 кВт•ч/т. Применение мельниц, использующих принцип раздавливания (вертикальные и горизонтальные), позволяет повысить производительность до 250…300 т/ч при снижении удельного расхода электроэнергии на помол до 24…28 кВт•ч/т. Однако сложность эксплуатации и ремонта, низкая эксплуатационная надежность сдерживает их дальнейшее распространение для помола цементного клинкера и добавок. Выводы и рекомендации Принципиально снизить энергоемкость процесса обжига при влажном сырье возможно при подготовке сырьевой шихты по мокрому способу. Затем, используя пресс-фильтры и ударные дробилки для обезвоживания шлама, можно снизить расход тепла на обжиг 950…1000 ккал/кг клинкера при расходе электроэнергии на весь печной агрегат 25…30 кВт•ч/т. В случае использования сухого сырья возможно применение сухой схемы производства клинкера с применением самых передовых разработок ведущих фирм-производителей цементного оборудования. При этом можно достигнуть расхода тепла на обжиг 800…850 ккал/кг клинкера. В качестве помольного агрегата целесообразно применять шаровые мельницы, усовершенствовав конструкцию ШБМ замкнутого цикла (сепараторы, внутримельничную футеровку, межкамерные перегородки и т. д.), а также технологические режимы в них (подготовка измельчаемой шихты, условия аспирации и сепарации и т. д.). C текущей ситуацией и прогнозом развития российского рынка цемента можно познакомиться в отчетах Академии Конъюнктуры Промышленных Рынков «Рынок цемента в России». Цемент. Известь. Гипс. |