Активные угли используют в многочисленных процессах предупреждения поступления в атмосферный воздух паров различных органических соединений путем их улавливания в целях как рекуперации (возврата в хозяйственный оборот), так и соблюдения действующих санитарных нормативов, а также в процессах очистки оборотных и глубокой доочистки производственных сточных вод. Представленные в настоящей статье разработки свидетельствуют о возможности обеспечения существенного прогресса в названных сферах. Они основаны на целенаправленных исследованиях, ориентированных на совершенствование потребительских свойств активных углей для обработки паровоздушных (парогазовых) потоков и жидких сред, позволивших осуществить разработку основ технологии углеродных адсорбентов новых марок. Эффективность практического использования данной продукции требует ее испытаний применительно к конкретным материальным потокам (объектам, средам), обычно сопряженных с необходимостью предварительных изысканий лабораторного уровня, также резюмируемых разработкой основ соответствующих сорбционных технологий. Ниже охарактеризован ряд таких разработок. Гранулированный активный уголь АГ-ПР для рекуперации паров органических и хлорорганических растворителей.
Дефицит активных углей для решения задач рекуперации растворителей составляет в России около 4000 т/год [1], причем одна половина этой потребности - это нужды производств искусственных волокон (ацетатных и вискозных), а другая - многочисленных производств в прочих отраслях промышленности. Наиболее остро стоит вопрос очистки газовых выбросов от паров фтор- и хлорорганических растворителей в связи с их особенно пагубным воздействием как на различные компоненты окружающей среды, так и на озоновый слой атмосферы. Углеадсорбционная очистка в данном случае наиболее приемлема ввиду нерациональности использования каталитических приемов в силу присущих им известных недостатков. Остра также проблема рекуперации паров высоко-кипящих (температура кипения - выше 100 °С) органических соединений. Наряду с этим совокупность адсорбционных и прочностных характеристик выпускаемых отечественной промышленностью активных углей в должной мере не отвечает задачам рекуперации широкого спектра органических соединений, присутствующих в парогазовых выбросах различных производств, что обусловливает актуальность разработки новых активных углей для совершенствования эксплуатационных показателей действующих и оснащения проектируемых рекуперационных установок. Взаимодействие органических и хлорорганических растворителей с пористой структурой активных углей на различных стадиях процесса рекуперации весьма специфично, поэтому необходима разработка рекуперационного угля с оптимальной структурой, наиболее полно учитывающей природу и свойства целевых компонентов соответствующих паровоздушных смесей. Рекуперационный уголь при развитых микропористой структуре и суммарном объеме пор должен обладать и необходимым объемом мезопор. Анализ литературных данных и результаты собственных исследований позволяют констатировать, что оптимальную структуру активного угля для рекуперации средне- и высококипящих органических и хлорорганических растворителей характеризуют параметры уравнения Дубинина-Радушкевича, имеющие следующие значения: W01 = 0,20÷0,35 см3/г, W02 = 0,10÷0,15 см3/г, Х01 = 0,5÷0,8 нм, Х02 = 1,0÷1,2 нм, или параметры уравнения Дубинина-Стекли, имеющие величины W°0 = 0,30÷0,35 см3/г, Х0 =0,6÷1,0 нм и δ>0,1. Многочисленными экспериментами авторов и результатами работ по рекуперации растворителей из паровоздушных смесей, выполненных другими исследователями, показано, что активные угли, полученные из слабоспекающихся и тощих углей методом парогазовой активации, характеризуют развитый (до 0,4-0,5 см3/г) объем и большой размер Х0 микропор при умеренных объемах мезо- и макропор [1]. Следует подчеркнуть, однако, что реакционная способность каменных углей низка. В случае же использования каменноугольного сырья с высокой реакционной способностью (длинно-пламенного и бурого углей или их полукоксов) развитие пористости (при идентичных условиях получения активных углей) идет в направлении преимущественного образования мезо- и макропор при сравнительно слабом (до 0,2 см3/г) развитии микропор. В этой связи при решении задачи получения активных углей с названными параметрами перспективно использование шихтования сырьевых композиций. Применение шихты из различных углеродсодержащих материалов позволяет управлять скоростью процесса активации и пористой структурой получаемого активного угля. Именно этот прием был впервые применен авторами при разработке технологии рекуперационных активных углей. Известно также, что одним из основных показателей процесса активации является величина обгара, определяющая не только выход готового продукта, но и, что особенно важно, развитие объема крупных микропор с размером поперечника 0,8-1,2 нм (при достижении пористости VΣ > 0,9 см3/г). Таким образом, качество получаемого рекуперационного активного угля оптимизировали изменением состава шихты и величины обгара, зависящей от времени активации. В качестве сырья использовали шихту из каменного угля (КУ) марки СС и полукокса (ПК) длиннопламенного угля марки ПК-1, измельченную в шаровой мельнице до частиц размером менее 90 мкм. Исследованиями авторов установлено, что лучшим связующим для такой шихты, обеспечивающим наиболее высокую прочность гранул продукта при истирании, является смесь лесохимической и каменноугольной смол в массовом отношении 70:30. Угольно-смоляную пасту гранулировали на шнековом прессе через фильеры с диаметром отверстий (3,5 ± 0,5) мм. Карбонизацию проводили во вращающейся электропечи при 450 и 750 ºС, активацию - в такой же печи при 900 °С смесью водяного пара и углекислого газа. Параметры пористой структуры этой серии образцов активного угля в соответствии с уравнением Дубинина-Стекли приведены в табл. 1. 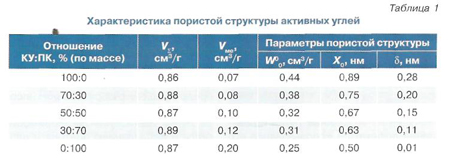 Анализ свойств пористой структуры и адсорбционной способности образцов полученных активных углей позволил сделать вывод, что шихтовая композиция, содержащая 50-70 % полукокса, обеспечивает при небольшом времени активации получение активных углей заданной микропористой структуры, обладающих достаточно большой прочностью при истирании (84-88 %). Охарактеризованные результаты положены в основу разработки технической документации на получение промышленной партии нового активного угля для рекуперации растворителей в условиях действующего производства активных углей типа АГ-3 и АГ-5. Партия продукта, изготовленного в ОАО «Заря» в количестве 10 т, полностью соответствовала техническим условиям на новый рекуперационный уголь марки АГ-ПР (активный гранулированный полукоксовый рекуперационный), технология которого запатентована (патент РФ № 20723191). Уголь этой партии испытан в Дзержинском филиале НИИОГАЗ в условиях многоцикловой работы, соответствующих эксплуатации адсорбентов в реальных рекуперационных процессах улавливания паров растворителей широкой номенклатуры. Условия испытаний: содержание паров в обрабатываемых потоках - 20 г/дм3, температура -25 °С, высота слоя гранул адсорбентов - 10 см, фиктивная линейная скорость обрабатываемых потоков - 0,2 м/с, температура десорбции - 105-110 °С, время десорбции - 60 мин, расход водяного пара при десорбции - 0,75 г/(мин-см2), фиктивная линейная скорость пара при десорбции - 0,06 м/с). Результаты этих испытаний (табл. 2) свидетельствуют, что реализуемая активность активного угля АГ-ПР вследствие его рациональной пористой структуры во всех случаях превосходит таковую типовых для рекуперационных процессов активных углей АР-А и СКТ-3. 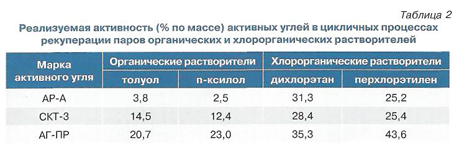 Наиболее важные процессы рекуперации с использованием активного угля АГ-ПР реализованы в производстве фильтрующего материала ФПП (фильтрующее полотно Петрянова) на предприятиях ОАО «Электростальский химико-механический завод» (г. Электросталь), ОАО «Заря» (г. Дзержинск), Серебрянский завод неорганических производств (г. Серебрянок). За период эксплуатации рекуперационных установок этих предприятий с использованием активного угля АГ-ПР предотвращен выброс в атмосферу более 3000 т дихлорэтана. Технология рекуперации дихлорэтана с применением активного угля АГ-ПР запатентована (патент РФ №2117521). Опытные активные угли для очистки технологических и сточных вод. Только в период 1998-2005 гг. авторами разработано около 30 новых активных углей, перспективных для использования в процессах очистки технологических и сточных вод (АГ-95-Р, АДБ, АДБ-В, АК-Ф, «Гидросорб-5», «Гидро-сорб-5-Р», КВ-3, КСВ, КСВ-3, КДС-СС, ПДС, ПДС-5, САУ-В, СКГ-3, СКД, ТПА, ТПА-6, УАФ-Р, ФТГ и др.). Оптимальные условия использования порошковых и гранулированных форм этих адсорбентов обоснованы исследованиями, выполненными в РХТУ им. Д.И. Менделеева применительно к реальным объектам очистки (оборотным потокам, сточным водам, конденсатам производств различного профиля) на образцах последних и (или) их моделях. Установленные при этом величины определяющих технологических параметров выдержаны при проведении на действующих производствах соответствующих испытаний, дублированных с сопоставительной целью аналогичными испытаниями с активными углями такого же назначения заводского производства (АГ-3, СКТ-3, УАФ и другие марки). Результатами выполненных производственных испытаний (в подавляю¬щем их большинстве) констатирована возможность альтернативного использования названных новых активных углей наряду с активными углями заводского изготовления для извлечения из воды и водных растворов нефтепродуктов, масел и других органических веществ, а также ионов тяжелых металлов. Во многих случаях отмечена и целесообразность такого использования в связи с определенными преимуществами (обычно кинетическими и (или) емкостными) активных углей новых марок по сравнению с таковыми, производимыми отечественной промышленностью. Наиболее значимые детали этих работ, представляющие, в частности, подробные характеристики конкретных объектов углеадсорбционной обработки, условий и результатов осуществленных производственных испытаний, содержат оформленные по их итогам двухсторонние акты. Исследованиями, выполненными в РХТУ им. Д.И. Менделеева, показана возможность получения и разработаны основы технологии эффективных углеродных и углеродминеральных адсорбентов из крошки выведенных из эксплуатации автомобильных шин, бракованных изделий и отходов резинообувных производств, шламов очистки сточных вод производств акрилбутадиенстирольных пластиков, отработанных патронных фильтров лакокрасочных предприятий, отходов органопластиков и брака изделий их них, ориентированных на использование на авиастроительных заводах, донных осадков шламохранилищ нефтехимических и нефтеперерабатывающих заводов, подсушенных на полях фильтрации осадков сооружений биологической очистки коммунальных сточных вод, косточек плодов и скорлупы орехов, гузапаи (остатков возделывания хлопчатника) и ряда других крупнотоннажных и практически не находящих использования производственных отходов. Приоритетность ряда этих технологий защищена А.с. СССР № 1791377, патенты РФ № 2133148, 2138443, 2138444, 2155157, 2162056. В прикладном плане изучены процессы сорбционной очистки (доочистки, в том числе до санитарных нормативов) производственных сточных вод, технологических растворов и конденсатов от различных органических (СПАВ, фенолов, растворителей, нефтепродуктов и их эмульсий) и неорганических (ионов тяжелых металлов - меди, ртути, цинка, кадмия, кобальта, хрома и других, соединений фосфора и фтора) загрязняющих веществ с использованием указанных адсорбентов. Полученные результаты положены в основу технологий, ориентированных на решение конкретных природоохранных и технологических задач ряда предприятий и организаций [1]. Наиболее значимые результаты разработок, выполненных в данном плане, защищены в основном отечественными охранными свидетельствами (А.с. СССР № 1188104, 1198013, 1641777), часть их кратко охарактеризована ниже. Так, не находящие использования отходы предприятий авиастроительного профиля в виде остатков (обрезков, лома, брака) конструкционных органопластиков (препрегов) и изделий из них (объем образования - 100— 150 т/год на каждом предприятии) состоят из различной толщины пропитанных эпоксифенольным связующим (в количестве до 5 % по массе) и отвержденных в соответствующих условиях пакетов полотен, сотканных из сверхпрочного высокомодульного (полиамидбензимидазольного) волокна. Исследованиями, выполненными по заданию ВИАМ (г. Москва), показана возможность переработки этих отходов методом химической активации с получением уникальных порошковых и гранулированных активных углей с задаваемой условиями переработки пористой структурой, характеризуемой преобладанием микропор или мезопор (максимальная поглотительная способ¬ность по бензолу и йоду составляет 940 мг/г и 70 % соответственно). Реализацией ключевой стадии этой переработки в укрупненных масштабах с использованием электропечи Дзержинского филиала НИИОГАЗ подтверждены закономерности, установленные исследованиями лабораторного уровня. Результаты выполненных разработок переданы ВИАМ для включения в планы реализации мероприятий по утилизации отходов на подведомственных и смежных предприятиях. Около 3 млн т практически не находящих использования нефтяных шламов размещены в шламонакопителях нефтеперерабатывающих и нефтехимических предприятий стран СНГ, обусловливая ряд серьезных проблем экономического и природоохранного плана. На примере донных осадков шламохранилищ ПО «Нижнекамскнефтехим», Новокуйбышевского завода синтетического спирта и нефтеперерабатывающего завода г. Рязани (АООТ «РНПЗ») показана возможность переработки этих отходов (путем однократного термического воздействия на них) на дешевые порошковые (размер частиц - менее 1 мм) углеродминеральные адсорбенты для очистки сточных вод от эмульгированных нефтепродуктов и связывания (фиксации, сбора) плавающих пленок нефтепродуктов различной толщины. Полученные адсорбенты характеризуют насыпная плотность, находящаяся в пределах 0,43-0,57 г/см3, удельные величины суммарной (VΣ), мезо- (Vме) и макропористости (Vма), составляющие соответственно, 0,55-0,78, 0,33-0,41 и 0,17-0,32 см3/г (что позволяет квалифицировать их как переходномакропористые поглотители), высокая гидрофобность (что обеспечивает практически 100 %-ную плавучесть в течение не менее 30 суток не только агрегатов, образуемых частицами адсорбентов с нефтепродуктами - сырой нефтью, маслами, дизельным топливом, бензином, но и частиц самих адсорбентов), низкая выщелачиваемость в воде (менее 0,0001 мг/л при суточном контакте с 80 г адсорбента), высокая зольность (63-75 %) и способность к фиксации 1 г адсорбента до 7 г плавающих нефтепродуктов в зависимости от их вида и толщины пленки. Результаты этих работ переданы заказчикам (ТОО «Синтезкаучук» и ПО «Нижнекамскнефтехим»). По полученным данным Центральным проектно-конструкторским бюро химического машиностроения (г. Санкт-Петербург) выполнены технико-экономические расчеты по опытно-промышленной установке производства углеродминерального адсорбента мощностью 100 т/год на площадке ПО «Нижнекамскнефтехим» и разработаны исходные данные на проектирование такой установки. Сточные воды ванн обезжиривания, очистки подвесок и гидрофильтра окрасочного участка завода «Прогресс» (г. Протвино) имеют щелочной характер и содержат СПАВ, нефтепродукты, органические растворители, взвеси и другие загрязняющие вещества в концентрациях, в 3-4 раза превышающих таковые действующих нормативов на прием сточных вод в городскую канализацию. Их очистка реагентными способами экономически нецелесообразна вследствие больших расходов соответствующих реактивов и в связи с этим требует изыскания альтернативных решений. Результаты предпринятого среди широкого круга адсорбционно активных материалов поиска наиболее эффективного поглотителя суммы названных органических загрязняющих веществ позволили установить, что им является активный уголь СКТ. Вместе с тем дефицитность и достаточно высокая стоимость этого угля обусловили целесообразность восстановления свойств отработанного (отходного) активного угля этой марки. В районе расположения завода «Прогресс» на ацетиленовой станции для очистки ацетилена от фосфина используют активный уголь СКТ, предварительно подвергнутый специальной обработке в целях развития его мезопористой структуры. В процессе названной очистки уголь накапливает фосфор в виде фосфорной кислоты. Отработанный уголь не регенерируют, в результате чего он образует отходы производства. Вместе с тем наличие в отработанном угле фосфорной кислоты делает особенно привлекательным его выбор для исследований с указанной целью, так как высокая растворимость фосфорной кислоты предопределяет при контакте сточной воды с углем ее переход в объем жидкости, обеспечивающий, по крайней мере, частичное снижение ее щелочности за счет нейтрализации и одновременное высвобождение мезопор угля. В то же время в виду реализации поглощения ПАВ у нефтепродуктов преимущественно на внешней поверхности угольных частиц в целях развития этой поверхности и увеличения тем самым сорбционной способности целесообразно измельчение гранул отходного угля. В связи с этим исследования выполнены с использованием порошка названного угля, полученного измельчением гранул последнего в дисковой мельнице и содержащего фракции менее 0,05, 0,05-0,1, 0,1-0,125, 0,125-0,17 и более 0,17 мм в количестве 31, 14, 7, 5 и 43 % по массе соответственно. Как результат проведенных исследований, наибольшую трудность при выполнении которых представило определение поглощения сульфонола и синтанола на фоне других загрязняющих веществ (потребовавшее разработки оригинальной методики - патент РФ № 2038584), предложена технология очистки усредненных в накопителе сточных вод окрасочного участка, обеспечивающая требования названных нормативов. Существо этой технологии составляет последовательная обработка определенного объема сточных вод при постоянном перемешивании заданными (расчетными) количествами препарированного (как указано выше) отходного угля (10 мин) растворами сульфата окисного железа (5 мин), известкового молока и полиакриламида (5 мин), завершаемая разделением фаз фильтрованием. Таким образом, разработанная технология не только обеспечивает решение поставленной задачи (свойственной большинству машино-, аппарата- и приборостроительных предприятий), но и вовлечение в материальное производство отходных углей СКТ. Результаты работы, пере- . данные заказчику, направлены для проектирования установки очистки производственных сточных вод окрасочного участка завода «Прогресс». На Подольском опытном заводе «Гиредмет» (Подольский химико-металлургический завод - ПХМЗ) при резке монокристаллических заготовок и отмывке (водным раствором моющего средства типа «Лотос») от шлифовальной пасты нарезанных кремниевых пластин при их шлифовании от грубого к тонкому образуются сточные воды, содержащие все компоненты шлифовальной пасты и моющего раствора, включая нефтепродукты в виде трансформаторного масла (25-50 мг/л) и механические примеси (до 100 мг/л). На основании исследований, выполненных с привлечением широкого круга адсорбентов, для эффективного решения задачи обеспечения требований, предъявляемых к качеству очищенных стоков (содержание взвешенных веществ, нефтепродуктов и ПАВ, не более 2,10, 0,17 и 2,50 мг/л соответственно), предложен тот же (что и охарактеризованный выше) модифицированный при очистке ацетилена от фосфина отходный уголь СКТ в виде порошка. Разработанная технология очистки названных сточных вод с использованием этого угля успешно апробирована на оборудовании отделения очистки производственных стоков ПХМЗ и передана этому предприятию для реализации. Реагентную очистку сточных вод производств АБС-сополимеров (АБС-пластиков) сопровождает образование весьма значительных количеств не находящих использования и удаляемых в отвал комкующихся пастообразных осадков. Массу осадков текущего выхода составляют: полимерлатекс - 5-10%, гидроксид алюминия - 4-5 %, древесная мука - 5-7 %, влага - 78-86 % и примеси неорганических соединений. Элементный состав органической составляющей образца воздушно-сухой пасты представлен углеродом (39,6 %), азотом (34,7 %), кислородом (20 %) и водородом (5,5 %), а состав его минеральной компоненты в оксидной форме характеризует наличие Al203 (91,9%), Fe203 (4,2 %), Si02 (2,7 %), S03 (1,0 %), Na20 (0,1 %), K20 (0,1 %). Отношение органической массы к минеральной в сухих осадках составляет (2,5÷3,4) : 1. Исследованиями показана возможность одностадийной термической переработки таких отходов на порошковые углеродминеральные адсорбенты, содержащие до 20 и 80 % соответственно углерода и гамма-оксида алюминия. Эти продукты, полученные в оптимальных условиях названной переработки сырья 60%-ной влажности (с массовым выходом около 35 %), представляют собой порошкообразный материал черного цвета, массу которого (в %) образуют фракции (в мм) менее 0,05 (8,7), 0,05-0,12 (31,6), 0,12-0,25 (19,7), 0,25-0,35 (8,0), 0,35-0,50 (12,0), 0,5-0,8 (9,4), 0,8-1,3 (5,7), 1,3-1,6 (4,9). Их характеризуют гравиметрическая плотность, суммарная пористость и удель¬ная поверхность, близкие 0,78 г/см3, 0,48 см3/г и 340 м2/г соответственно, а также ионообменная способность по 0,1 н. раствору NaOH (HCI) - 2,5 (2,1) мг-экв./г. Цилиндрические гранулы 6*6 мм, спрессованные из порошка адсорбента таблеточной машиной, имеют прочность при истирании 85 %. Лабораторные исследования сорбционных свойств этих поглотителей позволили констатировать возможность их эффективного использования для очистки разнообразных сточных вод от загрязняющих веществ органической и неорганической природы. Приготовление укрупненной опытной партии углеродминерального адсорбента осуществлено в обжиговой печи одного из цехов завода огнеупорных материалов, где названный отход, помещенный в специально подготовленные металлические контейнеры объемом 1 м3 с крышками, подвергли термообработке в близком к оптимальному режиме. Часть полученного порошкового углеродминерального адсорбента сформовали в виде гранул, которые использовали в целях очистки сточных вод машиностроительного завода г. Узловая (Тульская обл.). Порошковый адсорбент использовали для доочистки стоков очистных сооружений промышленного узла г. Узловая. В обоих случаях он обеспечил высокую степень извлечения ионов тяжелых металлов (от 80 до 100 % для большинства из них) и 33-100%-ную очистку от различных видов органических соединений, причем использование его порошковой формы более эффективно. Разработанная технология передана для внедрения Узловскому ПО «Пластик». Совокупность ряда охарактеризованных разработок отмечена дипломом I степени 2-й Международной специализированной выставки-форума «WASMA-2005» [2]. Более подробная информация о них опубликована в работах [1-3]. Литература 1. Мухин В.М. Активные угли России / В.М. Мухин, А.В. Тарасов, В.Н. Клушин. -М.: Металлургия, 2000. 2. Клушин В.Н. Отходы производства как потенциальное сырье для получения углеродных и углеродминеральных адсорбентов / В.Н. Клушин, А.Н. Хомутов, Д.В. Клушин // Тезисы докладов научно-технической конференции «Рециклинг, переработка отходов и чистые технологии» (Сокольники, 7.12.05). - М., 2005. С. 30-31. 3.Клушин В.Н. Получение адсорбентов из отходов, не находящих использования / В.Н. Клушин и др. // Экология производства. Химия и нефтехимия. 2006. № 2 (4). С. 3-6.
В.М. Мухин, докт. техн. наук, ОАО «ЭНПО «Неорганика», В.Н. Клушин, докт. техн. наук, А. И. Родионов, докт. техн. наук, А.Н. Хомутов, канд. техн. наук, Д.В. Клушин, канд. техн. наук, М.М. Статиров, А.С. Киреев, аспиранты, РХТУ им. Д. И. Менделеева
|