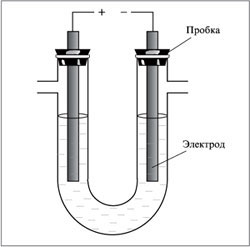
Н.В. Кулешов1, Н.В. Коровин1, А.А.Терентьев2, А.В.Рыжиков2 Московский энергетический институт (технический университет), Россия (1) ОАО “Уралхиммаш”, пер. Хибиногорский 33, г. Екатеринбург, Россия (2) 1. Электролитический водород: состояние проблемы в России 1.1. Электролизные установки для получения водорода производства ОАО”Уралхиммаш”
ОАО “Уралхиммаш” является одним из крупнейших предприятий отрасли химического машиностроения России; на его долю приходится почти 15% выпускаемого в стране оборудования. По некоторым видам продукции завод занимает монопольные позиции на российском рынке. Одним из таких направлений деятельности является производство электролизных установок для получения водорода. Предприятие является крупнейшим производителем щелочных электролизеров в России (ранее в СССР) уже более 50 лет. В табл.1 приведены основные характеристики электролизеров, выпускаемых заводом «Уралхиммаш». Кроме этого, предприятие производит мощные установки большой производительности: блочные установки производительностью по водороду до 250 нмЗ/ч, работающие под давлением и установки типа ФВ производительностью до 500 нмЗ/ч, работающие при атмосферном давлении. В целом, электролизное оборудование «Уралхиммаш» эксплуатируется более чем на 800 предприятиях России, 120 Украины, 50 Казахстана, около 30 предприятиях Беларуси, а также на ряде предприятий других республик бывшего СССР. Кроме того, осуществлялись крупные поставки в страны дальнего зарубежья (Болгария, Египет, Польша, Турция, Иран, Куба, Алжир, Индия, Марокко, Китай и т.д.). Таблица 1. Техническая характеристика электролизных установок типа СЭУ ОАО “Уралхиммаш” Наименование | СЭУ-4М | СЭУ-10-2 | СЭУ-20 | СЭУ-40 | Сила тока, подводимая к электролизеру, А | 330 | 2х1000 | 1000 | 1000 | Напряжение на электролизере, В | 72 | 50 | 105 | 215 | Рабочее давление, кгс/см2 | 10 | 10 | 10 | 10 | Рабочая температура, °С | 80±5 | 80±5 | 80±5 | 80±5 | Чистота газов, %: | водорода | 99,0 | 99,7 | 99,7 | 99,7 | кислорода | 98,0 | 99,5 | 99,5 | 99,5 | Производительность, нмЗ/ч: | по водороду | 4 | 10 | 20,5 | 41 | по кислороду | 2 | 5 | 10,25 | 20,5 | Габаритные размеры, мм: | длина | 1700 | 1650 | 2400 | 4100 | ширина | 610 | 2х1060 | 1060 | 1060 | высота | 830 | 1646 | 1780 | 1780 | Масса электролизера, кг | 1290 | 2х3390 | 4720 | 7435 | Масса электролизера с комплектующим технологическим оборудованием, кг | 10578 | 45191* | 23390 | 27335 |
* Масса двух электролизеров с комплектующим технологическим оборудованием и автоматизацией Основным недостатком таких электролизеров является высокое потребление электрической энергии. Так отечественные электролизеры имеют энергопотребление 5,0 – 5,3 кВт•ч/м3 Н2, а лучшие зарубежные образцы – 4,1 – 4,3 кВт•ч/м3 Н2. В настоящее время зарубежом возрастает потребление водорода, что привело к возникновению новых фирм производящих электролизеры нового поколения. Кроме традиционного использования в высокоразвитых странах, на деле осуществляющих защитные мероприятия по охране окружающей среды, возникают совершенно новые направления использования электролизеров, такие как производство водорода на автозаправочных станциях, аккумулирование энергии возобновляемых источников и другие. Создание новых высокоэффективных электролизеров с КПД более 80% предусмотрено государственными программами НИОКР многих зарубежных стран. В СССР, в связи с относительно низкими тарифами на электроэнергию, вплоть до середины 80-х гг. была экономически оправдана эксплуатация сравнительно дешевых электролизеров с невысоким КПД, разработанных в 50-гг. В этой связи, разработки ОАО «Уралхиммаш» по модернизации электролизных установок, которые проводились в 70 – 80-х годах были направлены в основном на улучшение надежности аппаратов и безопасности при их эксплуатации. Работы в области повышения энергоэффективности аппаратов новых типов практически не осуществлялись. Кроме того, вследствие большой износоустойчивости электролизеров (срок эксплуатации электролизного оборудования производства ОАО «Уралхиммаш» составляет 30 лет и более), а также нехватка финансовых ресурсов на воспроизводство, привело к тому, что сегодня многие предприятия продолжают эксплуатировать устаревшие энергоемкие установки. В настоящее время при росте тарифов на электрическую энергию затраты на производство водорода становятся весьма ощутимыми, а в некоторых случаях и обременительными, даже при производстве водорода на собственные нужды. С другой стороны, закупка любого западного электролизера требует достаточно серьезных инвестиций. А отсутствие дешевых высокоэффективных отечественных электролизеров тормозит развитие ряда высоких технологий. В этих условиях предприятия, использующие электролитический водород, вынуждены проводить регламентные и капитальные ремонты. Сегодня в нашей стране сложилась ситуация, когда практически отсутствует выпуск конкурентно способных электролизеров, и из экспортера этой техники Россия превращается в импортера. Уже имеются первые примеры закупок дорого стоящего западного оборудования. В то же время в стране существует серьезный рынок потребителей, который может повлиять на производство и дальнейшее развитие установок по производству электролитического водорода. Понимая данную ситуацию ОАО «Уралхиммаш» предпринимает определенные шаги по модернизации электролизного оборудования. В данный момент внедрен в производство новый односекционный щит управления и контроля на базе микропроцессорной техники, с выходом на удаленный персональный компьютер (взамен старого трехсекционного, выполненного на релейных схемах). Это позволяет дистанционно наблюдать за режимом работы электролизной установки в реальном времени и управлять производительностью электролизера путем изменения величины тока, подаваемого на электролизер. Организация производства более современных и энергоэффективных электролизеров тормозится отсутствием реальных опытно-конструкторских разработок в этом направлении. 1.2. Современное производство электролитического водорода В нашей стране электролитический водород применяется: - в пищевой промышленности в основном для гидрогенизации жиров. Промышленность ориентирована на крупные блоки по 250 нм3Н2/ч. Здесь сохраняется стабильная с точки зрения производства маргариновой продукции ситуация, но отмечается возрастание вклада себестоимости водорода в отпускную цену продукта. - в металлургии: а) для получения металлов методом прямого восстановления руды (электролизеры ФВ-500) б) для получения твердых сплавов. Исторически сложилось так, что каждый завод оснащался электролизерами СЭУ-40 , со средним количеством электролизеров 5-10 штук; - в электронной промышленности водород используется для создания восстановительной атмосферы. Одно из основных требований предприятий электронной промышленности к используемому водороду – его высокая чистота. Например, в некоторых процессах эпитаксии содержание примесей воды должно находиться на уровне не выше 0,01 ppm, что соответствует точке росы – 100ºС. Этим требованиям наилучшим образом соответствует водород, получаемый электролизом с последующей очисткой. К сожалению, в настоящее время электронное производство находится в стадии стагнации. Прежде производство электролитического водорода на предприятиях электронной промышленности составляло заметную долю в его общем балансе. Например, только в московском регионе находятся предприятия, потреблявшие следующие количества водорода на установках СЭУ-40: - предприятия г. Зеленограда – не менее 1000 нм3Н2/час; - подольский химико-металлургический комбинат - 2000нм3Н2/час; - остальные – не менее 1000 нм3Н2/час; - в энергетике водород используется для охлаждения мощных турбогенераторов, благодаря его высокой теплопроводности и коэффициенту диффузии, а также нетоксичности. Для этой цели на крупных ТЭЦ и АЭС создаются электролизные станции с расходом водорода около 6,10-3м3/МВт∙ч. Таким образом, станция содержит 2 электролизера (один резервный) производительностью 10 или 20 нм3Н2/ч. - в стекольной промышленности, где самым большим потребителем электролитического водорода (две станции – по 500 нм3Н2/час каждая на базе электролизеров СЭУ-40) является стекольный завод в г. Бор, Нижегородской области. Это предприятие традиционно обеспечивает стеклами отечественные автомобили, самолеты и постоянно расширяет свой ассортимент. На предприятиях, производящих жидкий водород, современные потребности в котором составляют около 2 тыс. т. в год; У многих мелких потребителей водорода в фармацевтической, металлообрабатывающей и других отраслях. В близкой перспективе необходимость увеличения производства электролитического водорода связана как с развитием его традиционных потребителей, так и с появлением новых, таких как автотранспорт, космонавтика, энергоустановки на основе топливных элементов, энергоустановки и системы преобразования и аккумулирования энергии на базе возобновляемых энергоресурсов и многих других. 1.3. Характеристики некоторых зарубежных электролизеров Среди зарубежных фирм, работающих в области электролиза воды, таких как Proton Energy Systems Inc., HSSI Electrolyzer, H2Gen Innovation Inc. и др., наибольший объем продаж имеют фирмы, ориентированные на щелочные электролизеры большой производительности. Значительные успехи в области их создания и реализации в настоящее время имеют фирмы Norsk Hydro Electrolysers (Норвегия), Stuart Energy Systems(Бельгия), Teledyne Inc. (США). Генераторы фирмы Stuart Energy Systems (Бельгия) производительностью до 120 нм3H2/ч состоят из двух блоков: источника тока и самого электролизера. Весо- и массогабаритные характеристики в десятки раз ниже аналогичных по производительности отечественных, поэтому они не требуют строительства отдельных зданий, поставляются полностью собранными в виде двух контейнеров. Аналогичные установки с несколько другой элементной базой производит фирма Norsk Hydro Electrolysers. Работа по внедрению электролизеров указанных фирм на нашем рынке только начинается. В качестве примера можно привести заключение контракта между Мосэнерго и Stuart Energy Systems о поставке электролизера производительностью 20 нм3 Н2/час для охлаждения турбогенератора одной из станций.
2. ПЕРСПЕКТИВЫ СОЗДАНИЯ ОТЕЧЕСТВЕННЫХ ВЫСОКОЭФФЕКТИВЫХ ЭЛЕКТРОЛИЗЕРОВ По виду электролита различают три основных вида электролизеров: (а) с водным щелочным электролитом (рабочая температура до 500 К); (б) с твердым полимерным электролитом (рабочая температура - до 423 К); (в) с твердым оксидным электролитом (рабочая температура - до 1300 К).
2.1. Электролизеры со щелочным электролитом Щелочные электролизеры, выпускаемые ОАО «Уралхиммаш» – это разработки 50–х годов, последняя модернизация которых выполнена в 80-е годы. Большая металлоемкость, значительное энергопотребление, наличие асбестового полотна делают эти электролизеры не конкурентно способными на мировом рынке. До сих пор ОАО «Уралхиммаш» остается монополистом в области создания крупных установок, хотя предпосылки для создания современных установок имеются, о чем говорят успехи в области разработок щелочных топливных элементов, которые по своей технической сути являются более сложными устройствами по сравнению с электролизерами. С целью замены асбестовой диафрагмы АТ-6 и дальнейшего вытеснения асбеста из электрохимических установок со щелочным электролитом, в качестве пористой диафрагмы нами исследованы: - диафрагма на основе асбокартона, разработанная специально для щелочного электролиза, взамен ткани АТ-6. Существует несколько способов получения микропористого асбокартона (бумаги) путем укладки различных волокон. По технологии, принятой в бумажной промышленности, готовят пульпу из коротких, распущенных до требуемой толщины волокон и отливают листы бумаги или картона на сетки - диафрагма на основе полисурьмяной кислоты. Снижение омических потерь на диафрагме, повышение механической прочности и улучшение разделительных свойств при электролизе воды достигается тем, что смешение порошков полисурьмяной кислоты и связующего проводят в среде этилового спирта при следующем соотношении компонентов, масс.%: полисурьмяная кислота 95-97, связующее (фторопласт-4, полисульфон) 3-5. Далее полученную суспензию напрессовывают на сетку и подвергают нагреву. − диафрагма на основе полисульфона марки ФПСФ-15-90 (толщина диафрагмы 0,3 мм; поры материала диаметром 8 мкм).
В табл.2 приведены удельные электропроводности вышеуказанных диафрагм. Таблица 2. Удельные электропроводности диафрагм Тип диафрагмы | Толщина, см | Концентрация КОН, моль/л | Уд. электропроводность, σ*102, Ом-1 см-1 | Раствор КОН | - | 6,4 | 54,3 | Асбобумага | 0,016 | 6,0 | 27,0 | Полисурьмянаякислота | 0,030 | 5,1 | 20,5 | Полисульфон | 0,030 | 6,0 | 19,0 | МФ-4СК | 0,025 | 4,5 | 3,75 |
Целесообразность введения дополнительного сепаратора между диафрагмой и поверхностью электрода (20-200 мкм) с целью создания электролизера с «нулевым» зазором обеспечит идея синтеза ЭДЭ (электродно-диафрагменного блока). Во всех случаях при создании электролизера с «нулевым» зазором предлагается нанести на поверхность асбобумаги и диафрагм на основе полисурьмяной кислоты лак МФ-4СК в виде пористого слоя. Ионообменные мембраны на основе фторсульфополимера («МФ-4СК», «Нафион») хорошо показали себя в процессах твердополимерного электролиза и при работе в водородно-кислородном топливном элементе. Однако исследования указанных мембран в процессах щелочного электролиза выявили их высокие омические сопротивления, вызванные, вероятно, затруднениями переноса иона щелочного металла (табл. 3) по сравнению с быстрым переносом протона, осуществляемым по эстафетному или солитонному механизму в твердополимерном процессе. С целью создания диафрагмы на основе лака МФ-4СК в его основу вводились как порообразователи, так и гидрофильные наполнители TiO2, Al2O3. В качестве растворителя лака МФ-4СК использовался изопропанол. В данном случае основной целью добавок является повышение создание пористой фазы в объеме органической основы так и повышение стойкости лакового покрытия «МФ-4СК» к действию кислорода. Использованные гидрофильные добавки TiO2, Al2O3 имеют долю в общем весе лака «МФ-4СК» в диапазоне от 3 до 50%. В табл.3 приведены некоторые физико-химические характеристики композитного материала на основе лака «МФ-4СК» с различным содержанием гидрофильных добавок. Таблица 3. Некоторые физико – химические свойства композитного материала на основе лака МФ-4СК
№ диафрагмы | Наполнитель | Максимальныйдиаметрпор, мкм | Пористость, % | Угол смачивания водойпо истечении суток | Уд. электропроводность σ*102, Ом-1 см-1 | вид | % масс | 0 | 2 | 30 | 500 | 1 | МФ-4СК* | - | 1,36 | 44 | 47 | 56 | 42 | 41 | 27,5 | 2 | МФ-4СК* | - | 0,92 | 46 | 49 | 55 | 43 | 42 | 28,3 | 3 | МФ-4СК* | - | 1,72 | 49 | 49 | 56 | 44 | 44 | 29,5 | 4 | Al2O3 | 3 | 0,92 | 47 | 50 | 56 | 45 | 44 | 22,3 | 5 | Al2O3 | 10 | 1,12 | 49 | 50 | 57 | 45 | 43 | 25,4 | 6 | Al2O3 | 30 | 1,56 | 56 | 55 | 58 | 50 | 49 | 27,5 | 7 | Al2O3 | 50 | 1,70 | 59 | 56 | 63 | 54 | 50 | 29,0 | 8 | TiO2 | 3 | 0,70 | 45 | 50 | 55 | 53 | 53 | 22,8 | 9 | TiO2 | 10 | 0,76 | 48 | 52 | 60 | 54 | 52 | 25,7 | 10 | TiO2 | 30 | 0,96 | 55 | 54 | 61 | 55 | 52 | 26,3 |
*пористая диафрагма на основе лака МФ-4СК, выполненная с удаляемым поронаполнителем Удельная электропроводность σ измерялась в растворе электролита КОН с концентрацией 6 моль/л. Предварительные эксперименты показали, что несмотря на большой разброс данных, существует принципиальная возможность получения образцов со сравнительно низким удельным сопротивлением. Объяснить это можно различиями в структуре диафрагм. Для проверки предположения была постав лена серия экспериментов по изучению влияния пористой структуры диафрагмы, изготовленной поливным методом, на ее показатели. Основным методом исследования была контактная эталонная порометрия, позволяющая получать распределение пор по радиусам в условиях смачиваемых и несмачиваемых рабочих жидкостей. Далее приготовленную диафрагму на основе модифицированного асбеста, полисурьмяной кислоты подвергают предварительной обработке в жидкости с низким поверхностным натяжением с последующей термической обработкой в печи при t=3000С в течение 30 мин. Приготовленную суспензию лака «МФ-4СК» с наполнителем наносят с помощью аэрографа на диафрагму в несколько приемов. После нанесения каждого слоя диафрагма подсушивается, после чего операция по нанесению повторяется. Следующий слой, наносимый на модифицированную диафрагму по аналогии с синтезом мембранно-электродного блока для твердополимерного электролиза, содержит катализатор на основе ренеевского никеля (ТУ 14-1-3790-88) и платины, равномерно распределенных в лаке МФ-4СК. ЭДЭ, минуя стадию горячего прессования, после предварительной подсушки проходит термообработку со скоростью 20 град/час с выдержкой при t=300 0С в течение 1 часа. Известно[2], что при щелочном электролизе анодные и катодные процессы имеют глубину протекания на порядок выше, чем при работе с твердополимерным электролитом, щелочная электрохимическая ячейка кроме ЭДЭ содержит сетчатые электроды. На рис 1 приведены поляризационные характеристики [3] анодов на никелевой подложке и подложке из нержавеющей стали после их активации методом циклирования в свободном объеме 6 М КОН при температуре 25 оС. На этом рисунке приняты следующие обозначения поляризационных кривых: 1 – сетка из нержавеющей стали 1Х18Н10Т, 2 – никелированная нержавеющая сетка; 3 – никелевая фольга гладкая; 4 - никелевая фольга никелированная; 5 – никелированная никелевая сетка; 6 – никелевая сетка с композитным покрытием без циклирования; 7- то же с циклированием; 8 - никелевая сетка с композитным покрытием; 9 − то же с содержанием палладия около 0,5 мг/см2 видимой поверхности электрода. Рис.1 Вольтамперные характеристики анодных материалов в 6 М КОН. 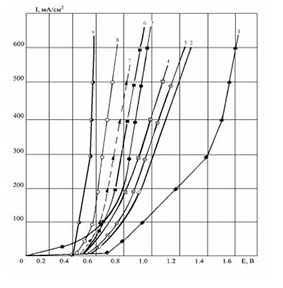
Как видно из рис.1, наилучшими характеристиками в реакции выделения кислорода обладали никелевые электроды с композиционным никелевым покрытием, содержащие небольшие количества палладия. Из данных рис.1 также следует, что при прочих равных условиях на параметры вольтамперной характеристики заметно влияет природа подложки. Электроды, в качестве подложки для которых использовался никель, значительно превосходят по активности электроды из нержавеющей стали. Этот эффект, по-видимому, можно объяснить образованием на нержавеющей стали оксидов с меньшей электронной проводимостью. С увеличением толщины никелевого слоя до 20 мкм влияние подложки из нержавеющей стали ослабевает, но остается все же заметным. Одним из возможных путей снижения стоимости электролитического водорода, как известно, является разработка и использование в электролизерах электродов – катализаторов с высокоэффективными, технологичными и недорогими каталитическими покрытиями. Разработан сплав Ni–Mо, который используется как самостоятельное каталитическое покрытие, так и в качестве подложки для многослойных катализаторов, а так же как составная часть ренеевских сплавов Ni–Al–Mo, Ni–Mo–Ti–Al, Ni–Mo–Zn, Ni–Mo–Si–Al–O. На рис.2 приведены поляризационные кривые (ПК) катодного выделения водорода на сетках из нержавеющей стали с покрытием Ni–Mo различной толщины. По сравнению с поверхностями без покрытия на никелированной поверхности наблюдается резкое снижение поляризации и уменьшение наклона начальных участков ПК. Рис. 2. Поляризационные кривые катодного выделения водорода на сетке из нержавеющей стали. 1 – без покрытия; 2 – никелированной (5 мкм); 3-6 – с покрытием Ni–Mo, (мкм): 3–4; 4–6; 5–7; 6–10; 7– 7 мкм Ni– Mo–S.
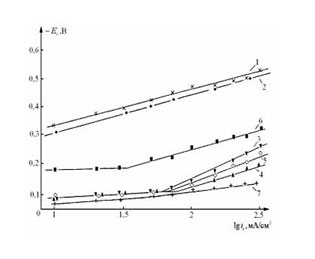 На рис.3 представлены зависимости напряжения электролизной ячейки от плотности тока и температуры. Вольтамперная характеристика (ВАХ) линейна, начиная с плотностей тока 150-200 mА/см2. Следует также отметить усиление влияния температуры с ростом плотности тока. При плотности тока 300 mА/см2 напряжение на ячейки составляет 1,7 В при температуре 80˚С, при этом в качестве анода использовалась никелевая сетка с композитным покрытием, а качестве катода – сетка из нержавеющей стали с Ni– Mo–S покрытием. Рис.3. Вольтамперные характеристики электролизной ячейки. Р = 0,1 МПа.
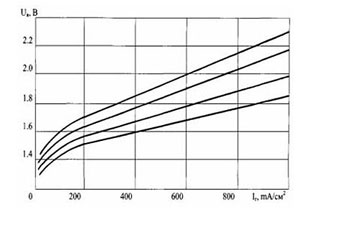
2.2. Электролизеры с твердополимерным электролитом В настоящее время областями применения электролизеров с твердополимерным электролитом (ТПЭ) являются аналитическое приборостроение, системы коррекции водно-химического режима атомных реакторов, водородная сварка, металлургия особо чистых металлов и сплавов, производство чистых веществ для электронной промышленности, аналитическая химия (оборудование для газовой хроматографии, обеспечение водородом лабораторий) и т.п. Результатом проведенных на протяжении 20 лет работ стало создание электролизеров с ТПЭ и установок на их основе различной производительности (от нескольких миллилитров до десятков кубических метров водорода в час) и назначения. К настоящему моменту накоплен значительный опыт по проектированию и изготовлению опытных и мелкосерийных образцов, имеются конструкторские и технологические разработки для изготовления элементов конструкции (мембрано-электродных блоков, коллекторов тока, биполярных пластин, уплотнительных элементов и т.д.). Разработаны электрокатализаторы на носителях, смешанные оксидные каталитические композиции, позволяющие снизить расход металлов платиновой группы без уменьшения ресурса. При этом показано, что активность композиции с 40-50 ат. % RuO2 сравнима с активностью чистого IrO2, а параметры электролиза с анодным электрокатализатором в виде RuO2(30%)-IrO2(32%)-SnO2(38%) при расходе платиновых металлов 0,8 мг/см2 практически сходны с параметрами электролиза с иридиевым анодным электрокатализатором и расходом 2,0-2,4 мг/см2. Рабочие характеристики электролизеров: энергозатраты 3,9-4,1 кВт×ч/м3 водорода при i = 1 А/см2 и t = 90°С и напряжении на ячейке U = 1,68-1,72 В, чистота водорода более 99.99%, рабочее давление до 30 атм., расход благородных металлов 0,3-1,0 мг/см2 на катоде и 1,5-2,0 мг/см2 на аноде, ресурс работы более 20000 ч. Существенный интерес представляет проведение электролиза воды с ТПЭ при повышенных давлениях. Исследования [4-6] показали, что при проведении процесса электролиза при повышенном (до 30 атм) давлении наблюдается улучшение вольтамперной характеристики при рабочих плотностях тока по сравнению с электролизом при атмосферном давлении. Это обусловлено, в первую очередь, снижением анодного перенапряжения. Так, при плотности тока 2 А/см2 на видимую поверхность напряжение электролиза уменьшается на 70-80 мВ. Кроме того, повышенное давление позволяет проводить электролиз при температуре выше 100°С, тем самым снижая энергозатраты за счет уменьшения сопротивления мембраны и снижения перенапряжения. В частности, при температуре 120°С и давлении 25 атм. при плотности тока 1 А/см2 видимой поверхности напряжение на ячейке составило 1,65 В. Таким образом, благодаря проведенным исследованиям удалось значительно повысить характеристики систем с ТПЭ. 2.3. Высокотемпературные электролизеры Высокотемпературный электролиз по своим термодинамическим параметрам превосходит низкотемпературные системы, указанные выше. Несмотря на успехи научно-исследовательских работ на уровне ячеек, создать промышленный аппарат до сих пор не удается. Основные трудности связаны с проблемами масштабирования проводящей по О2- керамической беспористой диафрагмы на основе диоксида циркония. НИОКР по созданию высокотемпературных аппаратов продолжаются, в основном, в ГНЦ «Физико-энергетический институт им. А.И. Лейпунского», Институте высокотемпературной электрохимии УНЦ РАН (г. Екатеринбург) и некоторых других организациях. 2.4. Заключение Сегодня из трех технологий щелочной электролиз воды остается основным методом крупномасштабного производства электролитического водорода. Однако, результаты исследований и разработок последних лет показывают, что электролизеры с твердополимерным электролитом уже в близкой перспективе могут стать серьезным конкурентом этой технологии. Сегодня в лабораторных условиях разработаны электрохимические ячейки с ТПЭ, обеспечивающие электролиз воды с КПД более 90% (энергозатраты менее 3,8 кВт×ч/нм3) при плотностях тока, на порядок превышающих таковые в щелочных электролизерах. Основные проблемы, которые необходимо решить при создании эффективных электролизеров с ТПЭ – снижение стоимости мембранно-электродного блока, увеличение ресурса и масштабирование процесса, то есть выход на большие единичные модули. В настоящее время в России имеется более 1000 предприятий, использующих электролизеры, произведенные на ОАО «Уралхиммаш» с 1983 по 1991 гг. В странах СНГ и дальнего зарубежья насчитывается более 100 предприятий, оснащенных аналогичными электролизерами. Поскольку проектный срок службы электролизеров ОАО «Уралхиммаш» составляет 10 лет, практически все электролизеры морально и технически устарели и подвергаются в настоящее время ремонтам различной степени сложности. Таким образом, уже сегодня в нашей стране существует потребность в большом количестве высокоэффективных и дешевых электролизеров. Только для замены устаревшего и энергоемкого оборудования необходимо создание нескольких тысяч новых аппаратов различной производительности. Приобретение электролизеров у зарубежных фирм потребует больших инвестиций и в близкой перспективе практически нереально. В этой связи разработки отечественных электролизеров с энергозатратами на уровне 4 кВт×ч/нм3 Н2 как со щелочным, так и с твердополимерным электролитом становятся особенно актуальными для развития водородных технологий в нашей стране. Список литературы
1. Шпильрайн Э.Э., Малышенко С.П., Кулешов Г.Г. Введение в водородную энергетику. М.: Энергоатомиздат, 1984, 264 с.
2. Кулешов Н.В., Коровин Н.В., Тельнов В.П. Водородная энергетика. Способы получения водорода для энергоустановок. М.: МЭИ, 1989, 50 с.
3. Коровин Н.В., Савельева О.Н., Удрис Е.Я. и др. Исследование электрокатализаторов катодного выделения водорода на основе малоуглеродистой стали. − Электрохимия, 1987, т. 23, с. 707.
4. Кулешов Н.В., Фатеев В.Н., Григорьев С.А Разработка электрохимических систем с твердым полимерным электролитом// в ж. Наукоемкие технологии, №10, 2004, с.85-89
5. Лютикова Е.К., Кирюхин Ю.И., Антонова Л.Л., Федышина К.В., Самойлов Д.И., Мотлох Ч.Г., Фатеев В.Н. “Разработка стойких к СО электрокатализаторов для твердополимерных топливных элементов” // Международная конференция “Электрокатализ в электрохимической энергетике”: Тез. докл. - Москва, 2003. - с. 21. 6. Халиуллин М.М., Кулешов Н.В., Григорьев С.А., Фатеев В.Н. Твердополимерный электролиз при повышенном давлении // Международный симпозиум “Гипотезис-III”: Тез. докл. - С.-Петербург, 1999. - С. 70 (на английском языке). Данная статья опубликована в Сборнике трудов Международного симпозиума по водородной энергетике. http://www.ekb.ru
|